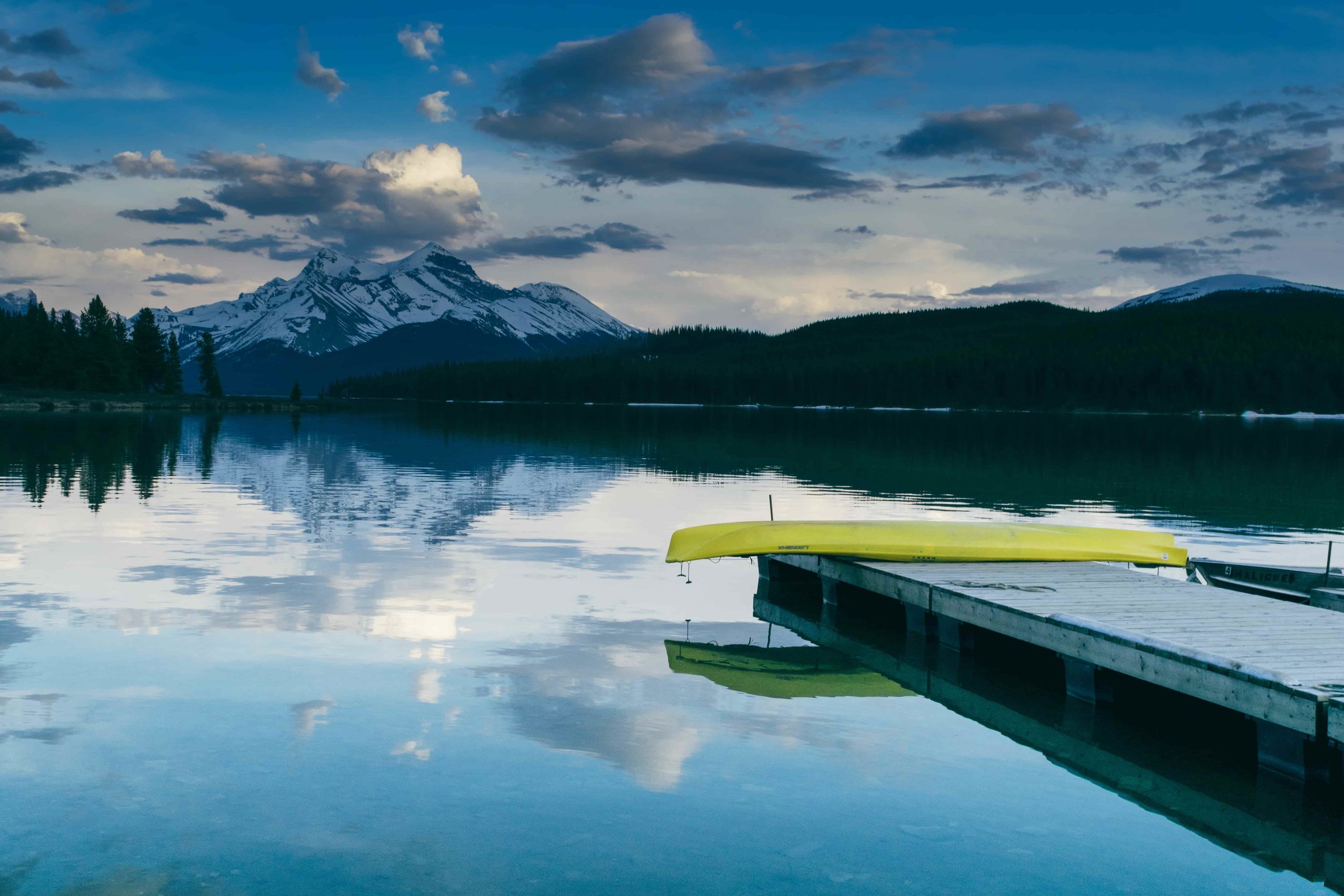
EL BLOG DE LA CADENA DE SUMINISTRO
Optimización de almacenes: Maximización de la utilización del espacio y reducción de costos
En el mundo de la gestión de la cadena de suministro, los centros de distribucion desempeñan un papel crucial en el almacenamiento y la distribución eficiente de mercancías. Sin embargo, muchas empresas se enfrentan a espacios limitados y un constante incremento de los costos de operación, lo que puede disminuir la productividad y la rentabilidad. La clave para superar estos retos reside en la optimización de los almacenes. Al maximizar la utilización del espacio y reducir costos, las empresas pueden obtener importantes beneficios y lograr una ventaja competitiva en el mercado. En este artículo, exploraremos estrategias y consejos prácticos para optimizar las operaciones del almacén.
En el mundo de la gestión de la cadena de suministro, los centros de distribucion desempeñan un papel crucial en el almacenamiento y la distribución eficiente de mercancías. Sin embargo, muchas empresas se enfrentan a espacios limitados y un constante incremento de los costos de operación, lo que puede disminuir la productividad y la rentabilidad. La clave para superar estos retos reside en la optimización de los almacenes. Al maximizar la utilización del espacio y reducir costos, las empresas pueden obtener importantes beneficios y lograr una ventaja competitiva en el mercado. En este artículo, exploraremos estrategias y consejos prácticos para optimizar las operaciones del almacén.
Realice un análisis exhaustivo de la distribución del almacén: Un paso crucial en la optimización del almacén es analizar la distribución actual para identificar ineficiencias y áreas de mejora. Tenga en cuenta factores como la densidad de almacenamiento, el flujo de productos, la accesibilidad y la seguridad. Mediante una evaluación crítica de la distribución de su almacén, puede identificar oportunidades para reorganizar las áreas de almacenamiento, implementar mejores configuraciones de pasillos y utilizar el espacio vertical de forma eficaz.
Adopte la tecnología y la automatización: La incorporación de soluciones tecnológicas y de automatización puede revolucionar las operaciones de su almacén. implementar el sistema de gestión de almacenes (WMS) adecuado puede agilizar el control de inventarios, la ejecución de pedidos, mejorar la precisión general y permitir nuevas mejoras. Además, tecnologías como el escaneado de códigos de barras, el etiquetado RFID y los sistemas automatizados pueden mejorar los procesos de picking y embalaje, reduciendo los errores humanos y ahorrando un tiempo valioso.
Dar prioridad a la gestión de inventarios y a la planificación de ventas y operaciones (S&OP): Es muy importante considerar la planificación de la cadena de suministro desde un punto de vista holístico, de principio a fin. Esto ayudará a la empresa en general a nivel estratégico y tendrá un impacto positivo en el funcionamiento del almacén gracias a una mejor gestión del inventario. El éxito de la S&OP y de la gestión del inventario es crucial para la optimización del espacio y la reducción de costo . Si se conocen los niveles de inventario, los índices de rotación y los patrones de demanda, pueden aplicarse estrategias que minimicen el exceso de existencias, reduzcan los gastos de transporte costos y maximicen el espacio disponible. Además, la adopción de una metodología de análisis ABC puede ayudar a priorizar los artículos en función de su valor y optimizar la asignación de almacenamiento en consecuencia.
Aplicar principios Lean: La aplicación de los principios Lean a las operaciones de almacén puede suponer mejoras significativas en la utilización del espacio y la reducción de costo . Técnicas como las 5S (Clasificar, Ordenar, Abrillantar, Estandarizar, Mantener) pueden mejorar la eficiencia en los puestos de trabajo eliminando residuos y creando un espacio de trabajo organizado y eficiente. Las metodologías Lean también promueven la implicación de los empleados, creando una cultura de mejora continua.
Optimizar las estrategias de asignación de huecos y preparación de pedidos: Las estrategias eficaces de asignación de huecos y preparación de pedidos pueden minimizar el tiempo de desplazamiento, reducir la mano de obra costos y mejorar la productividad general del almacén. Analice la velocidad de las SKU y los patrones de pedidos para colocar estratégicamente los artículos de alta rotación más cerca de las zonas de expedición, reduciendo el tiempo necesario para recoger y embalar los productos de alta demanda. Revise y ajuste periódicamente sus estrategias de asignación de ubicaciones para adaptarlas a la evolución de la demanda y los requisitos de la empresa.
Fomentar la colaboración con los proveedores: Colaborar estrechamente con los proveedores puede ayudar a optimizar las operaciones de almacén y reducir costos. Explore los programas de inventario gestionado por el proveedor (VMI) que permiten a los proveedores controlar y reponer directamente los niveles de existencias. Esto reduce los plazos de entrega, minimiza las roturas de stock y libera espacio en el almacén. Además, explore las oportunidades de cambiar la forma en que los proveedores envían los productos para agilizar los procesos de recepción y almacenamiento. Entre los posibles cambios se incluyen el embalaje, las etiquetas y las prácticas de cross-docking para reducir la manipulación.
La optimización de los almacenes es un aspecto crítico de la gestión de la cadena de suministro que puede reportar importantes beneficios a las empresas. Al maximizar la utilización del espacio, implementar procesos eficientes y aprovechar la tecnología, las empresas pueden reducir costos, mejorar la productividad y aumentar la satisfacción del cliente. Recuerde que la optimización de su almacén es un proceso continuo que requiere una supervisión, un análisis y una adaptación continuos a la evolución de la dinámica del mercado. Adoptando las estrategias analizadas en esta entrada del blog, puede adoptar un enfoque proactivo hacia la optimización del almacén, liberando todo su potencial y posicionando su empresa para el éxito en el competitivo panorama del mercado.
Introducción al picking dirigido por voz (VDP)
La tecnología de picking por voz consite en un equipo que permite a los trabajadores tener las manos y los ojos libres en el almacén. Actualmente se está convirtiendo en un nuevo estándar en los centros de distribución. Es utilizado principalmente para la logística de salida, pero puede aplicarse a cualquier proceso de almacenamiento. El picking dirigido por voz (VDP) aumenta la productividad general, la precisión y la seguridad en las instalaciones.
¿Qué es la captación de voz?
La tecnología de picking por voz consite en un equipo que permite a los trabajadores tener las manos y los ojos libres en el almacén. Actualmente se está convirtiendo en un nuevo estándar en los centros de distribución. Es utilizado principalmente para la logística de salida, pero puede aplicarse a cualquier proceso de almacenamiento. El picking dirigido por voz (VDP) aumenta la productividad general, la precisión y la seguridad en las instalaciones.
El VDP adapta la tecnología Bluetooth y se integra con el sistema WMS o ERP del almacén. En lugar de que un empleado lea la información de una lista de picking o un escáner, el sistema se comunica con el empleado a través de unos auriculares inalámbricos y le indica dónde debe ir en el almacén y qué debe recoger. El VDP también proporciona confirmación en tiempo real, eliminando la necesidad del escaneado físico y el registro de la información, lo que mejora la eficiencia.
¿Cuáles son los beneficios?
Reduzca los errores y aumente la seguridad
Como ya se ha dicho, la VDP crea un entorno manos libres. Elimina la necesidad de pulsar botones, registrar/interpretar información manualmente, etc. En su lugar, el empleado con los auriculares sigue las instrucciones de los comandos de voz y la información de audio que se registra directamente en el sistema WMS. Esto puede reducir el número de errores de picking que normalmente se producirían por errores humanos, gracias a la facilidad de uso que proporciona el VDP.
La seguridad en el almacén es el elemento más importante en cualquier instalación. Hay muchos factores a tener en cuenta, como los equipos de manipulación de materiales y otros empleados en la planta, que pueden provocar accidentes no deseados. La capacidad de VDP permite a los empleados ser más conscientes de su entorno cuando se desplazan por el almacén. Ya no se distraen leyendo su lista de picking o su escáner por todo el almacén y sólo tienen que centrarse en desplazarse con seguridad hasta su ubicación de picking.
Aumento de la productividad
Según Körber Supply Chain, la integración del VDP en el almacén suele generar un aumento de la productividad del 20-25%. La integración elimina inmediatamente la necesidad de papel adicional y dispositivos portátiles, lo que reduce el tiempo necesario para detenerse, leer y escanear artículos y listas de selección. En su lugar, escuchar y hablar permite al usuario realizar varias tareas a la vez durante el proceso de picking. Además, a medida que se recopilan datos, se puede aumentar aún más la productividad encontrando la ruta de picking más óptima. Esta información puede extraerse para reducir el tiempo de desplazamiento dentro del almacén. Este aumento de la productividad reduce la mano de obra necesaria para la preparación de pedidos, lo que permite reasignar los recursos donde sea necesario.
El VDP también se integra con robots de picking para aumentar aún más la productividad. Además de que un empleado utilice el VDP, los robots de preparación de pedidos utilizarán el tiempo medio de recogida y desplazamiento para garantizar que el recogedor y el robot estén justo a tiempo el uno con el otro. Estos robots proporcionan una función aditiva en el proceso de automatización.
Datos y mejora continua
Este método no sólo proporciona información en tiempo real, sino que al mismo tiempo recopila datos para ofrecer estadísticas útiles, como el tiempo que tardará en completarse la tarea y el número medio de artículos en la lista de picking. Estas estadísticas son importantes para la mejora continua en el almacén. El acceso a esta información garantiza que los recolectores lleguen a tiempo, a la ubicación correcta y, a mayor escala, mantener los KPI.
El futuro del PDV
A medida que los almacenes sigan introduciendo nuevas tecnologías, el uso de VDP seguirá creciendo, ya que aumenta la precisión sin sacrificar tiempo. Lo más probable es que la integración con robots de picking crezca en paralelo debido a su funcionalidad complementaria, aumentando aún más los estándares. La libertad que ofrece el VDP a una empresa le permite abordar otros cuellos de botella del almacén, como el control de calidad o el almacenamiento de existencias, reasignando la mano de obra de picking a donde sea necesario. No sólo aumentará la productividad en el almacén, sino que la VDP también ofrece a las empresas la posibilidad de basarse más en los datos, lo que es fundamental para el crecimiento y la mejora continuos.